Automotive industry in transition: why adaptive structures matter today
Published February 13, 2024
- Automotive
- Operating Model & Agility
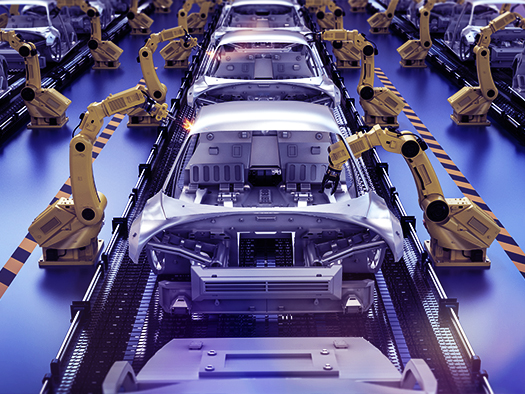
The automotive industry has long been characterized by stability and continuous innovation. Established product development processes and well-established supplier structures have driven the successful rise of German manufacturers. However, the industry is currently undergoing a significant transformation, facing a range of new challenges. These include the shift in powertrains, rapid digital transformation with a heightened focus on software, the need to meet climate targets, and the emergence of new competitors – be they innovative manufacturers from China or the major platform providers from Silicon Valley. In this changing landscape, the iterative improvements of the past are no longer sufficient. Instead, there is a need to question existing structures and embrace a high degree of flexibility to adapt and evolve.
Mutually amplifying challenges
As in many other industries, automotive manufacturers must develop a high level of adaptability, especially in terms of people, processes, and technology. However, they face a situation in which the individual challenges interact and amplify each other:
- Today’s structures for product development and product maintenance have evolved through continuous improvements resulting from past challenges. While they are highly efficient today, they are often not adaptable enough to meet changing conditions.
- The increasing complexity of the automotive product has created its own set of rules and framework conditions. This complexity tends to get in the way of fast and efficient adaptability.
- The iterative innovation cycles that have emerged from previous product development processes have led to the formation of strong silos within organizations. These silos solidify the existing organizational structure and hinder adaptive management of new tasks.
- Furthermore, software solutions break down these traditional silos and blur existing process boundaries. New topics such as over-the-air updates or post-bookable functions present challenges to established processes and structures.
In contrast, an adaptive organization is the key to maintaining a complex, software-defined product such as an up-to-date car throughout its entire lifecycle.
Three steps to creating an adaptive automotive organization
1. Mindset
People are central to driving change, from management to employees. To build the necessary adaptive and agile structures, break down silos, and redefine product development processes, cultivating the right mindset is crucial. At all levels of the organization, there must be an awareness that change is necessary and a willingness to implement it. Rather than solely focusing on key metrics, the focus should shift towards motivation. The goal is to preserve existing strengths while significantly increasing the organization’s adaptability.
Here’s how: responsibility for product components, processes, and functions should be organized end-to-end. The organization must establish guardrails for this and, if necessary, provide solution modules.
2. Processes
Automotive manufacturers are accustomed to thinking and planning within complex product contexts. Systems thinking remains valid and important even in a future dominated by digitization – but it must evolve into “end-to-end thinking“. Processes need to be further developed beyond their current boundaries or, where necessary, completely redesigned. Moreover, it is crucial to adopt a customer-centric perspective.
Here’s how: rethinking is required from the product development process to the customer journey. The objective must be to integrate changes into the product more quickly and provide customers with the best possible experience (customer experience).
3. Structures
When transforming the organization for greater adaptivity, it is important to not lose sight of its individuality. There is no one-size-fits-all approach to making an existing organizational structure more adaptive. It is sensible to begin this transformation process with an inventory and needs analysis, and then develop the future scalable and adaptive organizational structure based on that.
Here’s how: the transformation of the organizational structure should be approached as an iterative process. Trying to implement adaptivity comprehensively all at once is likely to fail. Instead, those in charge should focus on the fundamental elements and develop the transformation into an adaptive organization based on their adaptation to the new challenges and framework conditions mentioned earlier.
Automotive industry in transition: adaptability must be inherent in the system
In the automotive organization of the future, adaptability must be ingrained in the system. This necessitates transforming the existing structure in terms of people, processes, and technology to make it more adaptive. Key steps to evolve from the often-stagnant current state include cultivating the mindset of employees within the company, optimizing processes from product development to customer journey, and rethinking the organizational structure. These elements should be capable of effectively supporting digital opportunities in a scalable and adaptable manner.
Author
-
Stephan Blankenburg
Partner – Germany, Stuttgart
Wavestone
LinkedIn